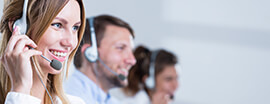
One of the foremost requirements for filling machines used in the dairy and protein powder industry is precision and accuracy. These powders are often sold based on their weight, and any deviation can lead to customer dissatisfaction and regulatory issues. Advanced filling machines are equipped with high-precision weighing systems that ensure each package contains the exact amount of powder specified. This accuracy not only maintains product consistency but also minimizes waste, contributing to cost savings for manufacturers.
Hygiene is paramount in the production of food products, especially those consumed by vulnerable populations such as infants and athletes. Filling machines for milk powder and protein powder must adhere to strict sanitary standards. This involves using materials that are easy to clean and resistant to contamination, such as stainless steel. Additionally, these machines often feature smooth surfaces and minimal crevices to prevent powder residues from accumulating, which can harbor bacteria.
Automated cleaning systems, such as Clean-in-Place (CIP) technology, are also a common feature. CIP allows for thorough cleaning of the machine's interior without disassembly, reducing downtime and ensuring a consistently sterile environment.
The ability to handle various types of powders and packaging formats is another crucial requirement for filling machines. Manufacturers often produce multiple products on a single line, necessitating equipment that can quickly switch between different powders and package sizes. Modern filling machines are designed with versatility in mind, featuring adjustable settings and modular components that allow for rapid changeovers.
Furthermore, these machines can be integrated with other packaging systems, such as sealing, labeling, and boxing, to create a seamless production line. This integration enhances overall efficiency and reduces the need for manual intervention, which can introduce errors and slow down the process.
Milk powder and protein powder can be very fine and prone to becoming airborne during the filling process, leading to potential contamination and health hazards. Effective dust control is essential to maintain a clean and safe working environment. Filling machines are equipped with dust extraction systems that capture and contain airborne particles, preventing them from spreading throughout the facility.
Additionally, many machines use enclosed filling mechanisms to further reduce dust generation. This not only protects the quality of the powder but also enhances the safety of the operators, reducing their exposure to inhalable particles.
To meet the demands of large-scale production, filling machines must be capable of high throughput while maintaining accuracy and hygiene. Advanced machines are designed to fill a large number of packages per minute, significantly boosting production capacity. High-speed filling is achieved through sophisticated control systems that coordinate the movement of powder and packaging materials with precision.
Efficiency is also enhanced by automated systems that reduce manual handling and streamline the filling process. For example, automated powder feeders ensure a continuous supply of material to the filling machine, minimizing interruptions and maintaining a steady production flow.
While advanced technology is essential for meeting the requirements of powder filling, user-friendly operation and maintenance are equally important. Machines should be designed with intuitive interfaces that allow operators to easily set parameters, monitor performance, and troubleshoot issues. Touchscreen controls and real-time data displays provide immediate feedback, helping to identify and resolve problems quickly.
Maintenance is simplified through the use of modular components that can be easily replaced or serviced. Preventive maintenance schedules and diagnostic tools help keep the machine running smoothly, reducing the likelihood of unexpected downtime.
Finally, filling machines for milk powder and protein powder must comply with various regulatory standards to ensure product safety and quality. This includes adherence to food safety guidelines such as the Hazard Analysis and Critical Control Points (HACCP) system, as well as compliance with local and international standards set by organizations like the FDA and the European Food Safety Authority (EFSA).
Manufacturers should ensure that their filling equipment is certified and regularly inspected to meet these stringent requirements. Compliance not only protects consumers but also enhances the reputation of the brand and reduces the risk of legal issues.
In conclusion, filling machines for milk powder and protein powder must meet a range of stringent requirements to ensure the accuracy, hygiene, and efficiency of the packaging process. By investing in advanced, versatile, and user-friendly filling equipment, manufacturers can enhance their production capabilities, maintain high standards of quality, and stay competitive in the rapidly growing market for powdered nutritional products. The integration of precision, hygiene, versatility, dust control, high throughput, user-friendly operation, and regulatory compliance ensures that these machines can meet the diverse needs of today's food industry.